The paper industry represents two percent of the world commerce and its demand has been increasing every day. Paper still is the main form of communication among people, especially in the education field. It also has an infinite number of industrial uses, amongst which we can mention those related with packing and health care.
The cellulose and paper industry uses around one third of total production of industry wood and this proportion is increasing. Two thirds of the fiber used to make paper comes from virgin fiber and the rest comes from waste fibers. Between 5 and 10% of the derivatives of the cellulose are produced based on fibers that do not come from wood.
Environmental concerns in manufacturing traditional paper
Amongst many environmental worries related to the manufacturing of traditional paper, we can mention:
- Biodiversity loss
- Replacement of natural or primary woods by tree plantations
- The insufficient use of waste paper and fibers that do not come from wood
- The domain of large scale mills that have a great political influence
- The continuous use of chlorine as a bleach
- Insufficient research regarding alternative technologies to produce paper in a cleaner way
- High levels of paper use which are not sustainable, especially in rich specially countries
- Systems of paper recollection and exports of paper impact the way of living of paper collectors in poor countries
- Excessive demand of transport in the commercial cycle of paper
- The hidden subsidies that promote the use of wood fiber rather than alternative fibers
Eco-paper
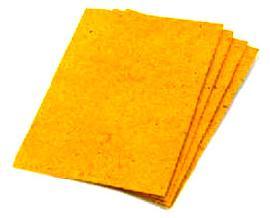
Agro-industrial fibres come from the waste of processing common agricultural industrial products. Ecopapers, specifically come with waste from bananas, mango, coffee, and tobacco. Research is currently involved into studying new fibres from pineapple, orange and palm hearts.
Each industrial process leaves different by by-products:
- Packing of bananas: as a result of pulling apart bunches of banana from the main stem, the pinzote is left over and it contains 5% of usable fibre to manufacture paper.
- Processing coffee: peels, leaves and small beans are separated from the coffee that will be processed, all this are used to manufacture coffee paper.
- By-products of tobacco: the leaves are separated from their veins during products the processes involved in the tobacco industry, and they are used to make tobacco paper.
Banana paper
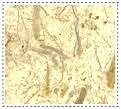
Banana paper is used in two different senses: to refer to a paper made from the bark of the banana plant, mainly used for artistic purposes, or paper made from banana fiber, obtained from an industrialized process, from the stem and the non-utilizable fruits. This paper can be either hand made or made by industrialized hand-made machine.
The banana agro-industry processes each year 42 million tons of bananas with 20,000 square kilometers plant. This industry generates numerous wastes such as: the plastic that wrap the bananas, plastic cords to tie the wrapping, damaged bananas and the stem The stems are composed of 92% water, 3% resins and 2% glucose, the rest is vegetable fiber.
This particular composition makes it decompose with the solid component not getting destroyed. This causes a severe impact on the surrounding ecosystems, the detriment of rivers and underground waters,also the massive reproduction of flies and nauseous smells. Agro-industrial fibers come from the waste of processing common agricultural products.
Packing of bananas: As a result of pulling apart the banana bunches from the main stem, we have the stems left over. These contain 5% of usable fiber to manufacture paper.
Steps in Production
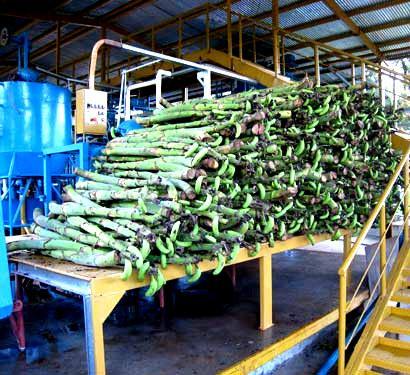
- Step 1 - Gathering the raw materials: It is composed of both 100% recycled post-consumer paper and agro-industrial waste. The post-consumer paper is obtained from offices, tetra pack containers, magazines and newspapers and sent to the mill. Then agricultural waste is collected from banana, coffee, lemon, mango, and tobacco plantations.
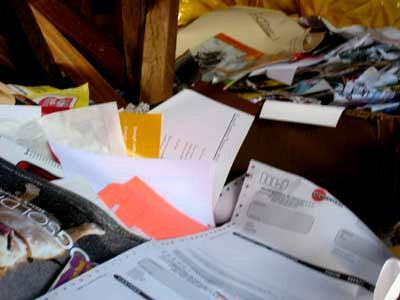
- Step 2 - Preparing the agricultural fiber: The scraps from the trees and left over fruits are first ground down until they resemble sawdust, turning into pure agro-industrial fibers. The fiber is washed to remove natural resins that would cause unnecessary binding, possibly fouling the machines, and taking away from the integrity of the paper.
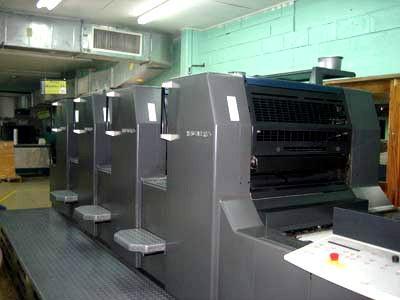
- Step 3 - Preparing the post-consumer fiber: Once the mill process has begun, the collected paper is thrown into the pulper along with water. The two are squashed and churned until the paper dissolves into the water. The process is called pulping and produces what is called the vehicle which means it is the base fiber in the paper for the agro-industrial fiber to be added.
- Step 4 - Mixing the two to create the final product: Mixing the post-consumer paper with the agro industrial fibers begins with putting the two products through a sprinkling system and an endless band and that acts as a sieve and keeps the pulp in suspension. The speed of the band and pressure of the sprinkling system dictates the thickness of the paper which can be 60, 90, 120, or 250 grams. The paper is then threaded into a set of drums and another endless band, made of absorbent material to further dry the paper. At the end of this process the paper will only retain 3% water and will receive natural coloring to provide attractive shades to the paper.
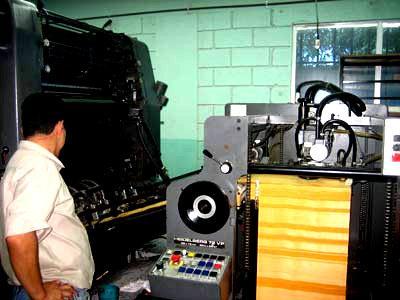
- Step 5 - The editorial and conversion process: One of the final and most complex processes of production, the editorial and conversion processes will determine the shape and aesthetic quality of the paper. It involves processes like rewinding and converting that prepares the paper to be cut into the shapes yielded in the shapes finished product. Skilled artisans cut and assemble decorative on on-lays and labels, laminating covers and assuring a top notch product.
- Stage 6 - The packing process: To ensure quality, strict packing standards are practiced, cutting down on waste by using only necessary and high quality packaging materials. Barcode identification is used to simplify warehouse accounting, leading to less headaches and more time to work with paper.
Mango paper
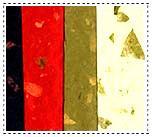
Mango paper is a slight variant of Chiri Paper and is handmade. Chiri papers are made with the help of long kozo fibers and mulberry barks. The same ingredients are used when making mango paper, but instead of mulberry barks, kozo fibers are included in a proportion of 60:40. These papers are made in abundance in Thailand and India, and are light in weight, semi transparent in nature and are very delicate. They are also available in a variety of colors, but are usually made in variations of yellow and green. The color of the paper depends on the variety of mango used. Usually the mango leaves are added as fragments and these leaves shine in light all over the paper. These papers have a level pH 6 which makes them slightly acidic. Mango paper is used to decorating crafts, collages, letterpress, book arts, etc.They are also great for printing invitations, gift wraps, lampshades, screens, table cloths and what not. The sweet smell and the taste of mango are retained and is what makes them special.
Steps in production
- Anyone can make Mango paper. All you need is a window frames, two picture frames, water, paper bits or kozo fibers, gelatin, and mango extract.
- Attach the first picture frame with the window frame with the help of a duct tape or staple gun all along the four sides and turn the screen upside down
- Now place the second picture frame over the first frame. The size of the Paper will be the size of the second frame.
- Now, tear the paper into pieces and mix it with hot water and gelatin in a blender. Allow it soak for half an hour.
- Add mango pulp and mix it in a blender till it becomes a smooth paste.
- Now, pour the pulp into the second frame and make sure there are no holes and the pulp is evenly spread.
- Lift the frames to drain if there is any excess water through the screen. Remove the top frame and topple the pulp on to a paper towel and leave it to dry.
- After it dries up, your sweet smelling and tasting mango paper is ready for use
Eco-paper Advantages
Due to the design, concept and the environmental philosophy surrounding the products,there are many strengths:
- It is an original product
- It is an attractive product: its beautiful design shows hours of dedication.
- It is an environmentally friendly product
- It is of very good quality and elegant
- It is a new concept
Financial assessment
- Plant capacity: 1.50 Ton/Day
- Plant & machinery: Rs. 17 Lakhs
- Working capital: Rs. 30 Lakhs
- T.C.I: Rs. 95 Lakhs
- Return: 41.42% Break even: 52.56%
Together with all the attributes mentioned above, there are many opportunities related to the commercialization of these products
- It is a market not yet exploited to its full potential
- There is a growing market for green products
- There is an ever-growing need for environmental awareness
- Developed countries show more concern for the environment
- Little competition from similar products
Equipments required
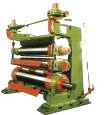
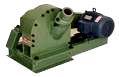
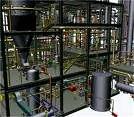
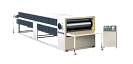
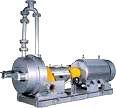
Source : Science Tech Entrepreneur Magazine, March 2011 issue